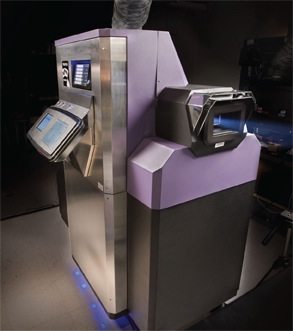
At the end of February when the FDA approved a variance clearing the way for Kodak to sell their laser projection technology to cinema exhibitors we ran a post which started out stating it was meant to be a competitor to Texas Instruments DLP chip. It didn’t take long for a commenter to point out that the Kodak’s system actually uses the DLP chip.
I spent considerable time searching through all of Kodak’s marketing material and press releases trying to find any reference to TI’s DLP chip and came up empty. Multiple searches on Google, that bastion of all knowledge, finally turned up some information which seemed to confirm that Kodak employed DLP in its solution.
All of this made me realize how little I actually knew about Kodak’s laser technology. I figured there could be no better source for information on the system than Kodak itself. Thankfully, I was able to speak with Les Moore, Kodak’s chief operating officer for Digital Cinema, who managed to shed some light (no pun intended) on the new technology. Surely, my first question should come as no surprise.
Celluloid Junkie: After being corrected in a recent post about Kodak Laser Technology and its use of the DLP chip I found it difficult to determine conclusively whether you are actually using the chip. Are you?
Les Moore: Yes. What we did was we said, “Lasers are starting to hit a price power point that makes some sense for theatrical use. Let’s see what we can do to design a projector using lasers as the light source. Let’s take a good hard look at the benefits that lasers can bring to a projector and then optimize the projector to make use of the lasers. There are a few manufacturers out there making good products in the industry with DLP, let’s base it around a DLP engine.” So that’s what we did.
CJ: The reason I ask is that there is no reference to DLP in any of your marketing or technical material. Was that intentional?
LM: I thought we had said it. I don’t believe it is described in the FDA variance. You might be right. There was no intent to not include that information. I think you’re aware we’ve held some open sessions here in Rochester where folks can hear a presentation that walks through the technology from front to back and then we take people up to a theatre and do a demonstration. It’s been very clear in those presentations that it’s designed around a DLP. Maybe that’s something we need to work on. It wasn’t intentional.
CJ: What incentive do the DLP manufacturers have to make laser projection available to the market when they are presently installing their xenon based d-cinema projectors as fast as they possibly can? Wouldn’t they be undermining their own interests?
LM: Whenever a manufacturer of products has a product line they have to manage that portfolio. So it’s a fair question. You’ve got to decide when you’re going to invest in new technologies, when you’re going to launch another round of products. You’d be challenged if you said you were just going to ignore future products, but on the other hand you have to launch them at the right time. So I think what a manufacturer needs to do is look at the technology and ask what it brings to the customer and how quickly they can bring it to the customer and then internally make that decision. I have an array of xenon DLP products, they’re growing in the marketplace, on the other hand we’ve got some technology that’s ready to be commercialized at this point, brings significant value to exhibition. A manufacturer has to make that call as to whether they want to be the first one out with it or whether they want to wait a little longer. I’m not inside those companies heads but it’s kind of general product management. New technologies are always coming along, you’ve got to decide when you’re going to launch them.
CJ: Does the the exclusivity of the TI DLP chips to Barco, Christie and NEC hinder the development of Kodak’s laser technology?
LM: We pulled together some technology. We implemented in a proof of concept prototype projector. An important thing to do with technology, right? You want to make sure it really works. And we demonstrated that it does here on site. What we’re interested in doing is licensing that to those in the industry that can make use of it. Outside of digital cinema DLP devices are used in projection devices by a large number of companies. Within D-Cinema, then there’s three companies that can launch DLP based products into that space. Our technology is not limited to digital cinema. It’s technology. It describes how you would incorporate lasers into a projection. Perhaps in the digital cinema space there are some constraints but certainly outside the digital cinema space those same constraints do not exist.
CJ: The studios are only offering VPFs up until a certain date, after which time most of the exhibition industry will already have been converted to xenon digital projectors. It will take them a number of years to pay those off. How does Kodak expect theatre owners to afford another digital revolution while the first one hasn’t even been paid for yet?
LM: We pulled a projector together and we’re licesning this to other manufacturers. Those manufacturers need to manage their product flow. If you’re an exhibitor what we’ve essentially done is given them another piece of data that they have to consider as they make the decision to move to digital. Prior to this they could say digital projection brings certain capabilities and new efficiencies to my booth. On the other hand, print film continues to be reliable and effective and a majority of audiences around the world are seeing great films and hearing great stories on motion picture film. An exhibitor now has to say there is some other technology coming. What we’ve done is prove that lasers are viable in the booth and they bring a lot of benefits to the theatre owner.
CJ: What are some of those benefits?
LM: Well, at a high level, total cost of ownership. It has higher brightness. It has built in 3D. When they originally designed the d-cinema DLP projectors 3D wasn’t a big portion of the business so they designed a great 2D projector. Well, lasers have 3D built in. And of course there’s been image quality improvements made by adding lasers. But let me provide some detail.
When you look at total cost of ownership, one thing you want to think about is if you want to simply replace the xenon light source, well yeah you’d have a laser projector at that point, but on the other hand you wouldn’t be able to take advantage of all the things that laser could bring to the equation. What the team did was redesign all of the optics in the projector. They went through and replaced the TIR prism with some very simple glass plates. So they reduced the cost of that section significantly. As well, a standard digital projector lens is fairly large physically and has a very low f-number. It’s a very fast lens so it’s very expensive. Our team replaced that lens with higher f-number lens because we don’t need the f-number and something that’s actually very small. The lens is a few inches long by an inch-and-half in diameter. So it’s a very small lens at a lower cost. So by adding lasers the cost of the projector is increased a little bit because lasers are more expensive than xenon. On the other hand if you can reduce the cost of the rest of the optics you can compensate for that in terms of the manufacturing cost. Then you have to think lasers are going to last 30,000 or more hours if they are properly cooled and if the design is done well. Lamp is 500, 1000 or 1,500 hours and exhibitors are replacing them multiple times per year. There’s enough elements here that are really changing the cost equation in a significant way that the exhibitor can take advantage of.
On the image quality side you certainly, with lasers, have a wider color gamut. So you’ll be able to represent more colors than a conventional xenon system will be able to represent. It actually ecompases the entire film space, which is significant. And then contrast ratio. Conventional xenon projector today has a white to black ration of 2,500 to 1 and we’re getting 10,000 to 1 or greater with this projector and you really notice it. You see these details in the blacks that in the conventional projector are crushed.
On the brightness side, most of the 3D systems out there use polarization to differentiate the left eye and the right eye. Lasers are hinherintely polarized. If you design your optical system to manage that polorization carefully, you’ve just removed one of the major inefficiencies in today’s 3D systems.
CJ: Can the Kodak system hit 14 foot lamberts in 3D on a 30 foot screen?
LM: Well, I can tell you what we did. We have an 11,000 lumen projector. Not a very big projector really. On a 40 foot silver screen we get 8 foot lamberts through the glasses to the eye for 3D. We’re very comfortable saying that this design could scale to 40,000 lumens, four times the brightness. If you chose to put that size of a projector on a 40 foot screen, clearly you’d have plenty of light. I guess you could argue that you could go from 8 foot lamberts to 14 foot lamberts by having one-and-half times the brightness.
CJ: Is there a limit to how big a screen can be used with Kodak’s laser technology?
LM: Not that I can think of. If you’re at 40,000 lumens you’re probably in that 60 foot screen range. Today’s xenon projectors, the big ones are 30,000 lumens. We’re comfortable we can go beyond that. I haven’t done the math on how big a screen size you can go to. We’ve more looked at it as what’s a reasonable screen size. Up to 60 feet we’re comfortable. I don’t see any fundamental reason why you couldn’t go beyond that.
CJ: How does the Kodak system deal with speckle?
LM: Speckle is one of the big issues with laser systems. The short answer is there is no one single method used to resolve speckle. The research guys here would build up a projector and introduce a solution to reduce speckle and it would reduce speckle, but it wasn’t gone. So they’d come up with another clever idea and add that in. There are probably half a dozen different things they’re doing in the projector that cumulatively have managed to reduce speckle to the point where you don’t notice it subjectively. You’re satisfied with the picture as you watch the movie and are comfortable with it. If you hear folks say that they’ve eliminated speckle, that speckle is totally gone, I think maybe what they’re saying is they’ve reduced it to a point where it’s subjectively not there, but to reduce it to zero that’s a different statement. We’re not actually saying it’s zero, we’re saying subjectively it’s reduced to a point where we’re comfortable with it. Studios and a number of folks who have come through, they don’t notice it.
CJ: Is the Kodak laser technology backwards compatible? Can it be installed in the DLP projectors currently being rolled out?
LM: The approach we took was not one of backwards compatability. We redesigned the entire optical system of the projector. I don’t think it would really be practical to be field replacing the entire optical system of the projector. There are other companies exploring that kind of space of where they are essentially replacing the xenon bulb with a laser light source. Now you don’t get all the benefits. You don’t necessarily get higher contrast ratios or built in 3D. You may actually have to work on how you do your speckle reduction. But you do of course get the long life lasers and that’s certainly an important piece. I think it’s a fair approach and I think there will be companies that deploy those types of systems.
CJ: Some have described Kodak’s solution as disruptive technology. Would you agree?
LM: That’s a good question. It has a couple of parts to it. On the market side and how the market develops, we’ve already discussed that. But as a pure technology, lasers are a breakthrough technology. Suddenly you’re able to change the equation a little bit in terms of long life. I know folks have been working on making longer life xenon bulbs and they make small changes. This is dramatic. Suddenly you’re to 30,000 hours. With contrast it took another leap from 2,500 to 1 to 10,000 to 1. So I wouldn’t say it’s a disruptive technology, it’s more of a dramatic technology. It’s providing significant capabilities to the marketplace that weren’t available before.
CJ: Will it really take two-years to bring the solution to market?
LM: We’ve commercialized products in the past at Kodak. Our judgement is that once a licensee says go, you’re looking in the 12 months to 24 months kind of range. It’s hard to predict a little bit. I think in the FDA release we said up to two years and that’s probably fair.
CJ: Are there any limitations on the FDA variance you recently received?
LM: First off, this a breakthrough in a sense that there’s never been such a variance. The FDA defined rules for laser projection for laser light shows and there are a number of constraints around those. The laser systems go through an FDA approval and the site where the lasers are being used goes through an approval. Then on a show by show basis, each time that display company is going to run their show, they need to get an approval. That’s kind of the sequence in the laser light space. What we did was say, “Look, creating new FDA regulations working through those kinds of legalities could take a long time. Let’s see if we can work under the constraints of laser light shows, but get a variance to remove some of those obligations, obviously with some boundary conditions, but enabling us to put a Kodak projector into a theatre and show movies.” The variance that we receives said, “We’re okay with you doing that. We’re willing to release the obligation of having a site approval by the FDA and release the obligation of a having a show approval.” A theatre that purchases a projector with Kodak technology does not need to have site variances and does not need to have show variances.
The variance is on the FDA website so anybody can pull it down and review it. It speaks to things like installation by authorized personnel so it’s installed a certain way, to specific training that’s required of theatre and booth personnel, it speaks to the minimum distances around the booth. You don’t want to have it such that a person can get within inches of the projection lens. Think about it this way, coming out of a lens, the lens is maybe an inch-1/2 in diameter inch and a quarter. So You’ve got all that light coming out of there and it’s very concentrated, but by the time it gets to the screen it’s spread over a very large area. Between that actual lens output and the screen it’s diverging very rapidly. Some of the analysis that the FDA did and some of the folks here did was to look at when are you far enough distance away from that lens so that the beam is diverged sufficiently that the power per square inch is low enough.
CJ: In some countries there are government or authoritative bodies checking all laser projection installations being used for entertainment purposes. Manufacturers must supply drawings and specs related to an installation before equipment can go in. Will this be same in future projector installations internationally. Will there be any limiting issue for installations?
LM: We didn’t do international. That’s another hurdle to cross. We’ve got FDA variance, now you’ve got similar agencies in Europe and perhaps some others in Asia. They’ve got different constraints.
- Edinburgh Filmhouse Secures 25-Year Lease, Announces New Patrons - July 11, 2024
- Mixed Results for Global Box Office During First Half of 2024 - July 10, 2024
- George Rouman, Cinema Operator and Industry Champion, Dies at 51 - June 13, 2024